La préfabrication, un standard en atelier ?
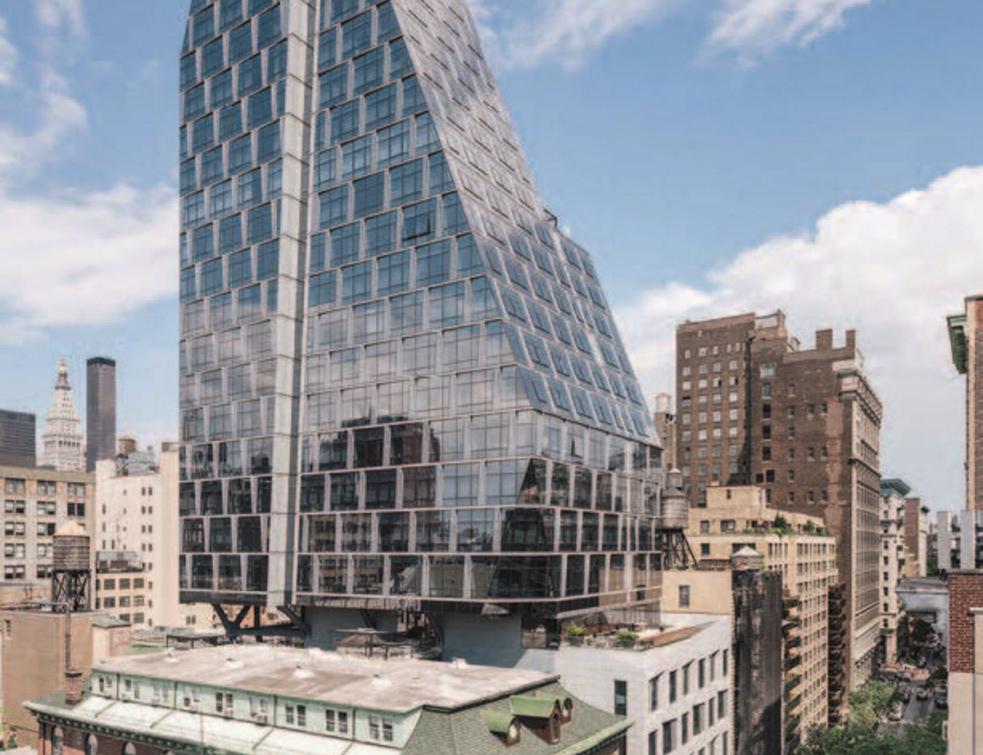
Le prêt-à-poser prend peu à peu sa place parmi les industriels et les artisans poseurs. Mais le sur mesure nécessite de travailler très en amont des projets afin de coller aux caractéristiques techniques demandées.
Tout est une question de timing : combien faudra-t-il d’années avant que la préfabrication n’inonde totalement les ateliers des gammistes et des menuisiers poseurs ? Tendance de fond depuis une dizaine d’années, le prêt-à-poser s’est en effet installé progressivement dans le monde de la menuiserie pour répondre à une équation simple : comment accélérer et faciliter la mise en oeuvre tout en garantissant et en préservant la technicité des produits ? Si aujourd’hui, la préfabrication concerne essentiellement les fenêtres et les baies coulissantes, certains industriels vont déjà plus loin en proposant de véritables systèmes, y compris pour la façade. Les fabricants, s’ils continuent de fournir des profilés à des artisans qui vont façonner des produits à façon, épousent désormais les tendances du marché qui va vers une séparation des activités de fabrication d’une part, et de pose de l’autre. Car les artisans fabricants poseurs, à l’instar de ce qui s’est opéré il y a quelques années déjà dans le secteur du bois, sont pour certains devenus des préfabricateurs qui ont délaissé la conception pour se cantonner à la mise en oeuvre. « Il existe depuis 2008 une tendance à la spécialisation du marché où il faut désormais distinguer la préfabrication de la pose », constate Pierre Dammé, directeur commercial de Sapa, le spécialiste des menuiseries en aluminium. « Il existe donc désormais d’un côté, les clients traditionnels qui font de la fabrication et de la pose, et de l’autre, les industriels et les préfabricateurs qui pour leur part font du prêt-à-poser. Nous suivons donc la tendance du marché en adaptant nos produits à une nouvelle typologie de clients qui disposent de petits ateliers désormais dédiés uniquement à la pose de produits préfabriqués dont ils choisissent les spécificités sans être contraints de rentrer un produit de gammiste ».
© Sapa (Groupe Hydro)
Pierre Dammé, directeur commercial de Sapa
Un réseau national de préfabricateurs en régions
Dans le groupe Hydro auquel appartiennent également les marques Wicona et Technal, Sapa a clairement été identifiée comme celle étant dédiée aux préfabricateurs, réservant aux entités soeurs les marchés premium et grands projets. Pour l’industriel, qui vend également du profilé en marque blanche via son entité Askey, la mise en place il y a quatre ans du réseau "Solutions Pro Sapa" s’est donc imposée comme une évidence. Ce réseau national de préfabrication de menuiseries aluminium destiné aux artisans poseurs et aux fabricants-installateurs possède aujourd’hui une vingtaine d’adhérents en région, réunis pour leur première fois lors d’une convention en juin dernier. Intérêt pour ses membres dont le profil est relativement identique (structure modeste et orientée à 80 % vers la rénovation) : partager de l’information et échanger sur les pratiques tout en étant rattachés à une marque reconnue.
Mais pour l’industriel Sapa, ce réseau d’indépendants sert également ses propres intérêts puisqu’il permet des remontées d’informations techniques pour améliorer en amont ses produits. Exemple : d’ici la fin de l’année, le fabricant va faire des modifications sur son ouvrant caché en 70 mm afin de mieux répondre à la demande de performance thermique. Pour l’heure, les profilés aluminium livrés à son réseau, mais aussi aux autres poseurs, proviennent du site intégré Sapa basé à Puget-sur-Argens (83), lequel site réalise le filage, le laquage et le stockage.
Ce procédé permet d’installer jusqu’à 250 m² de façade par jour et par équipe ! La conception flexible du système modulaire Wictec EL evo répond à toutes les exigences architecturales et s’adapte individuellement en rénovation à l’architecture existante de tout bâtiment. La taille des modules peut atteindre jusqu’à 3,5 m de haut x 2 m de large ou 3,5 m de haut x 3 m de large avec montant intermédiaire
L’outil de production a donc été calibré pour épouser les contraintes de la préfabrication pour usiner rapidement des menuiseries, tout en garantissant la performance à l’eau et à l’air d’un produit comme la fenêtre. « La difficulté, mais aussi l’avantage dans la préfabrication, consiste à reproduire des performances à l’identique en calibrant des produits selon les mêmes standards techniques invariants », poursuit Pierre Dammé. « Les produits qui se préfabriquent le mieux sont aujourd’hui la menuiserie à frappe ou coulissante, mais aussi les portails, les volets battants ou encore les garde-corps. La notion de transportabilité est également un point important dans la préfabrication car nos clients livrent leurs propres menuiseries et doivent être en mesure de les acheminer facilement sur site. Pour cette raison, la préfabrication est très bien adaptée au marché de la rénovation de la maison individuelle et beaucoup moins à celui des grands projets dans le tertiaire ». La préfabrication consiste donc d’abord pour Sapa en un large choix de produits conçus aussi bien autour des critères de performances que ceux portant sur les finitions. Ils sont donc de ce fait parfaitement adaptés au marché très divers de la rénovation. « La préfabrication permet de prendre de l’avance sur la concurrence car elle se positionne clairement sur la mutation du marché », conclut Pierre Dammé. « Le maillage de la solution aluminium reposait essentiellement sur des artisans fabricants poseurs. Désormais, le marché du prêt-à-la pose est en totale mutation et nous devons en tant qu’industriel offrir les produits qui répondent à ces nouveaux enjeux, au risque de rester sur la touche ».
Un point de vue que partage également l’industriel Reynaers qui s’est lancé à plein dans les menuiseries préfabriquées. Si l’ensemble de son activité préfabrication représente à peine un chiffre d’affaires de 2,8 M€ sur une enveloppe globale de 50 M€ (soit 6 %), Reynaers travaille néanmoins avec un réseau d’une quarantaine de préfabricateurs. Une petite dizaine fait partie du cercle restreint et est poussée par Reynaers à monter en capacité industrielle afin de devenir de vrais acteurs de la préfabrication. Sa valeur ajoutée : l’accompagnement pour encourager les entreprises à s’ équiper en centres d’usinage.
© Sapa (Groupe Hydro)/ Fab’Alu
Préfabricant depuis 2012, Fab'alu a rejoint le réseau Solutions Pro Sapa depuis fin 2020 ; le dirigeant François Herault a équipé son atelier de 400 m² de nouveaux outils pour fabriquer la gamme; Performance 70 de Sapa. Proche de Clermont-Ferrand, aux Martres-d'Artière (63), Fab’alu s’inscrit dans la logique d’une chaîne de valeur qualitative
Pousser à l’industrialisation des ateliers
Reynaers a ainsi fait le choix de travailler avec la marque Fom et épaule pendant plusieurs semaines l ’ entreprise qui accepte de revoir son outil de production. Mise à l'énergie, mise en place des liaisons informatiques entre le logiciel de saisie et l’atelier, prise en main, tout est fait pour pousser à installer des ateliers de prêts-à-poser dans un marché très concurrentiel où la différence repose sur la productiv ité. « Il est aisé enpréfabrication de créer des prototypes mais la vraie valeur ajoutée consiste à proposer un accompagnement complet de l’industrialisation de l’atelier afin que l’outil de production soit le plus efficient possible », note Romain Arnaud, chef de marché gammes industrielles en charge du développement des solutions prêts-à-poser chez Reynaers.
« L’objectif est de favoriser le développement du prêt-à-poser dans un marché très concurrentiel pour nous et pour nos clients et où la différence se fera sur la compétitivité. Développer ce marché, c’est aussi vendre davantage de matière première ».
Afin que les produits soient montés le plus rapidement possible, l’industriel propose des notices de conception agrémentées pour certaines gammes comme IndusLine ou IndusPatio, de vidéos qui dissèquent l’assemblage de la manière la plus industrielle possible. Si ces supports sont là pour enseigner comment monter le plus rapidement possible un produit tel qu’une fenêtre, reste que le résultat ne perd pas pour autant en technicité. Reynaers a d’ailleurs lancé une série de tests sur ses profilés de préfabrication qui montrent que les résultats en termes de performances acoustiques et thermiques sont identiques à des menuiseries qui ne rentrent pas dans la catégorie des gammes industrielles. « Le plus gros challenge consiste donc à ne pas dégrader le produit dans ses performances et à améliorer les produits par rapport aux temps de montage », souligne Romain Arnaud. « Pour y parvenir, nous livrons à nos clients du monobloc, tous les profilés sont préjointés avec un maximum de matière afin de réduire au minimum le nombre d’équerres pour l’assemblage. Nous faisons en sorte de rationaliser les profils afin qu’ils puissent être utilisés dans plusieurs cas, ce qui permet in fine au préfabricateur de ne pas cumuler des références dans son atelier ». En termes de productivité, les résultats eux aussi répondent à l’appel : entre 20 % et 30 % de gains par rapport à des gammes standards.
Du temps gagné grâce à des profils qui arrivent déjà jointés en atelier, mais aussi grâce à la suppression du vissage des tapées sur les ensembles monoblocs. Sans compter la quinzaine de minutes gagnées avec la fin du nettoyage des angles. Au final, le gain peut atteindre 45 min. sur ces trois opérations sur un montage basé sur une moyenne de 2h15. Un temps considérable au vu de la raréfaction de la main d’oeuvre sur les chantiers et de la difficulté à motiver des opérateurs à réaliser des tâches considérées comme ingrates car redondantes. Si Reynaers croit en la préfabrication, il vise néanmoins encore plus haut et ambitionne de tripler son chiffre d’affaires en préfabrication à l’horizon 2027. Un objectif basé sur un constat : la préfabrication permet de fidéliser les clients, mais aussi d’augmenter les débits.
© Sapa (Groupe© H Byodtrtoe)r/o SV Miroiterie
Adhérent Solutions Pro Sapa, SV Miroiterie est implantée à côté de Caen. Fabricant et poseur de menuiseries aluminium et miroiterie depuis 50 ans, l’entreprise accompagne des projets de vitrage haut de gamme et revendique un service de pose ad hoc
Banaliser la préfabrication aluminium
Reste à régler un écueil de taille : l’artisan ne saisit pas d’emblée la nécessité de s’équiper en centre d’usinage lorsqu’il a l’impression qu’il perd la main sur un outil de travail préformaté. D’autant que la rigueur au niveau de l’atelier dans des structures relativement simples n’est pas acquise. Reste que les artisans qui travaillaient le PVC voient désormais dans la préfabrication aluminium un moyen de gagner des marchés. Les entreprises qui sont déjà dans la fabrication PVC sont en effet aujourd’hui plus enclines à aller vers la préfabrication aluminium où comme dans le PVC, les joints et les tapées sont prémontées. Le cahier des charges de ces gammes préfabriquées a d’ailleurs été pensé pour permettre un montage comme du PVC. Et certains artisans veulent se développer dans l’aluminium avec du prêt-à-poser pour le particulier. « Le meilleur moyen de banaliser le produit préfabriqué est de le rendre équivalent au montage à du PVC, d’autant que la quincaillerie est identique, ce qui permet de rationaliser les accessoires et de limiter les stocks », explique Romain Arnaud. « La perte de vitesse du PVC est donc une chance pour la préfabrication aluminium. Certains clients proposent désormais des fenêtres aluminium préfabriquées au même prix que des produits en PVC. La préfabrication a donc une carte à jouer dans ce contexte économique tendu sur les matières premières où le prix de l’aluminium n’a pas connu la même hausse vertigineuse ».
© Reynaers
L’industriel Reynaers pousse son cercle de partenaires préfabricateurs à monter en capacité industrielle et accompagne l’entreprise qui le souhaite à revoir son outil de production pour installer des ateliers de prêts-à-poser dans un marché très concurrentiel
Optimiser les temps de mise en oeuvre et améliorer les niveaux de finition, c’est aussi le credo du vendéen Louineau. Le spécialiste des pattes de fixation s’est lui aussi lancé dans la préfabrication de précadres de fixation qui possèdent un ensemble de cornières soudées étanches facilitant la pose. L’industriel propose également des précadres d’habillage soudés et thermolaqués qui permettent de faire directement la finition entre la menuiserie et la façade, venant ainsi remplacer la partie bavettes d’habillage. « L’avantage de la préfabrication est d’arriver avec des éléments en un seul morceau et qui sont en plus autostables », note Guillaume Dufaix, responsable de la R&D chez Louineau. « Cela permet de limiter les interfaces entre les lots en appréhendant en amont les problématiques qui peuvent apparaître notamment sur les tolérances de support. Tout ceci permet au final de limiter les temps de reprise en site occupé, ce qui est appréciable quand les cadences de pose sont très élevées ». Si la préfabrication représente encore une part relativement faible de l’activité industrielle de Louineau, reste que son intérêt ne pose plus question.
© Cyril Badet Louineau
Le spécialiste des pattes de fixation Louineau a fait de son système de précadre Precwood une vitrine de son savoir-faire en matière de préfabrication, comme sur cet immeuble de logements à Issy -Les-Moulineaux
Un nouveau service pré-usiné chez Profils Systèmes Guadeloupe
(2e à partir de la gauche) Pascal Gaboriau, responsable Profils Systèmes Guadeloupe
Profils Systèmes Guadeloupe, spécialiste de la menuiserie aluminium dans les Caraïbes, a ouvert cette année son service de pré-usiné afin de proposer à ses clients menuisiers et poseurs des produits fabriqués sur mesure et prêts-àmonter. C’est dans son nouvel atelier de 150 m² que Profils Systèmes Guadeloupe, filiale du gammiste aluminium montpelliérain, propose à l’ensemble de ses clients des frappes, coulissants, portes et jalousies en aluminium prêts-à-poser. Deux couleurs sont disponibles en Profils Color : Blanc 9016 et Gris Anthracite 7016. Un gain de temps considérable, puisque les menuiseries sont livrées sur mesure et prêtes-à poser. Profils Systèmes dispose d’une base logistique en Guadeloupe destinée aux menuisiers aluminium locaux et des îles des Caraïbes. Cette base logistique se situe dans la Zone de Commerce Internationale, près du port autonome de Jarry à Baie-Mahault, poumon économique de la Guadeloupe.
© Aurélien Brusini / Architectes : Christian Nancey, |
Préfabriquer versus uniformiser
Demeurent toutefois certaines précautions. De fait, la préfabrication demande une étude très en amont des projets. « L’idéal de la préfabrication est d’établir un état des lieux du chantier sur lequel cela va être posé », poursuit Guillaume Dufaix. « Sur le stockage, il est notamment nécessaire de faire de la place sur le chantier où il va falloir cadencer correctement pour accueillir des éléments préfabriqués qui sont toujours plus volumineux que des éléments en kit. Si la préfabrication laisse le droit à l’erreur, l’important est de pouvoir l’anticiper et livrer dans les temps. Le segment de la réhabilitation se prête ainsi très bien à la préfabrication, notamment en site occupé où il faut éviter au maximum les nuisances pour les résidents. En réduisant les temps de pose, on réduit aussi de fait les aléas sur chantier ». A ces avantages et à ces précautions, il convient aussi d’ajouter que la préfabrication s'adapte parfaitement à la maquette numérique. Un atout certain alors que le BIM n’est plus un outil dont peuvent désormais se passer les industriels lorsqu’ils travaillent sur des produits en 3D.
© Franck Deletang
L’immeuble de services et bureaux Flow, développé par Covivio à Montrouge (92) bénéficie d’une façade par élément constituée de 2 400 modules ayant fait l’objet de développements spécifiques par les équipes Wicona et Facal.
Les évolutions sont ici concentrées sur les éléments techniques, constitutifs du module de façade. Cette nouvelle version permet la réalisation d’ouvrages intégralement fabriqués et prémontés en atelier, prêts-à-poser lors de leur arrivée sur chantier
La mutation de la préfabrication bâtiment, Wicona l’a également vue venir. Notamment en cette période de crise sanitaire durant laquelle les entreprises de pose ont été contraintes de s’adapter en fabriquant des chantiers de manière simultanée après une période d’arrêt plus ou moins importante. Une situation qui perdure aujourd’hui et qui a rebattu un jeu de cartes dans lequel la préfabrication est devenue une pièce maîtresse pour assurer les chantiers lorsque les capacités de production sont à leur maximum. Si la préfabrication chez Wicona concernait déjà les solutions feu, des produits spécifiques particulièrement adaptés en raison de leur technicité réglementairement encadrée, l’industriel travaille déjà sur des produits respirants préfabriqués.
« La préfabrication ne consiste pas à uniformiser, elle vise au contraire à garantir un savoir-faire », précise Vincent Bes, directeur commercial de la zone ouest chez Wicona. « Une petite structure qui fabrique quelques portes coupefeu chaque année n’a pas forcément les moyens humains et financiers pour les fabriquer. Cela nous pousse à faire des efforts pour assurer le process de fabrication en amont. Dans le produit respirant comme dans le produit coupe-feu, la fabrication est là pour répondre à la conformité. Nous observons aujourd’hui une vraie mutation sur le marché de la préfabrication bâtiment, avec des industriels qui font l’acquisition de préfabricateurs spécialisés pour apporter des réponses spécifiques sur certains projets. Cette tendance va aller en s’accentuant, avec des produits finis parfois très techniques et très encadrés ». Wicona a par ailleurs fait le choix de ne pas se positionner sur le marché de la préfabrication résidentielle trusté principalement par le marché du coulissant et de la fenêtre. Il s’est ainsi orienté vers le segment de solutions sur mesure qui portent sur des dimensions de menuiseries importantes, des remplissages lourds, ainsi que sur des solutions techniques comme le feu et le respirant.
Le must du module préfabriqué en façade
Fidèle à ce précepte, Wicona commercialise depuis avril dernier son nouveau système de façade par éléments baptisé Wictel EL Evo. Reprenant l’idée de modules sur mesure préfabriqués en atelier, le module dispose d’un nouveau joint à ressort permettant d’absorber les flèches de planchers ainsi qu’un système de drainage pour l’évacuation contrôlée de l’eau. Ainsi que le précise la documentation technique de Wicona, le système se base sur des profilés composites en aluminium à haute isolation thermique avec une taille de modules qui peut atteindre jusqu’à 3,5 m de haut x 2 m de large ou 3,5 m de haut par 3 m de large avec montant. Les masses d’aluminium réduites de la façade Wictec EL Evo (35 mm de large pour le profilé périmétral et 60 mm pour les montants et traverses) offrent plus de transparence et de luminosité et confèrent à l’ensemble des lignes fines.
Clairement destinée aux immeubles de grande hauteur, cette solution préfabriquée qui peut se résumer par emboîtement entre eux de gros châssis fixés indépendamment en façade de bâtiment favorise une mise en oeuvre beaucoup plus rapide sur chantier. « Une heure de fabrication en atelier coûte moins cher qu’une heure sur le chantier, d’autant que la façade cadre se met en oeuvre beaucoup plus facilement qu’une menuiserie traditionnelle », résume Vincent Bes. « Nos clients ayant des plannings de plus en plus serrés en matière de temps d’intervention, ce module répond parfaitement à la nécessité du temps court. Il faudra cependant veiller en amont à bien définir les dimensions exactes de profils ainsi que leur couleur, car le temps de fabrication est bien plus court que le temps de pose. Deux mois de production à l’avance sont ainsi nécessaires pour suivre la cadence de pose sur chantier ». Et Wicona a fait ses calculs : une équipe de deux opérateurs est en mesure de poser 250 m² de façade cadre par jour. Une surface qui selon l’industriel peut aisément être doublée avec du personnel rodé et expérimenté. Un avantage certain notamment pour fermer rapidement un bâtiment pour permettre aux autres corps de métier d’intervenir plus rapidement.
© Patrick Loubet
Wicona privilégie les élements préfabriqués de grande portée, notamment sur le centre aquatique de l'Estuaire à Saint-Nazaire avec des profilés Wicstyle. La halle aux cinq bassins (1 267 m2 de plans d'eau) ouvre sur les plages extérieures et le parc paysager par une façade sud-est entièrement vitrée sous trois toitures façon sheds, entre lesquelles s’intercalent des éclairages zénithaux – Coste Architecture
« Toutes nos solutions sont préfabricables car nous apportons la réponse la plus pertinente face à la problématique du chantier », conclut Vincent Bes. « Nous possédons les solutions techniques pour répondre avec des performances thermiques et acoustiques adaptées, des charges importantes et de grandes dimensions. Le marché de la préfabrication est en train de se lever, avec notamment des produits spécifiques pour les préfabricateurs de demain. La massi ficati on de l’industrialisation n’en est donc qu’à ses débuts ». Dont acte.
© Imagen Subliminal (Miguel de Guzmán + Rocío Romero)