L’extrusion face à de nouveaux défis
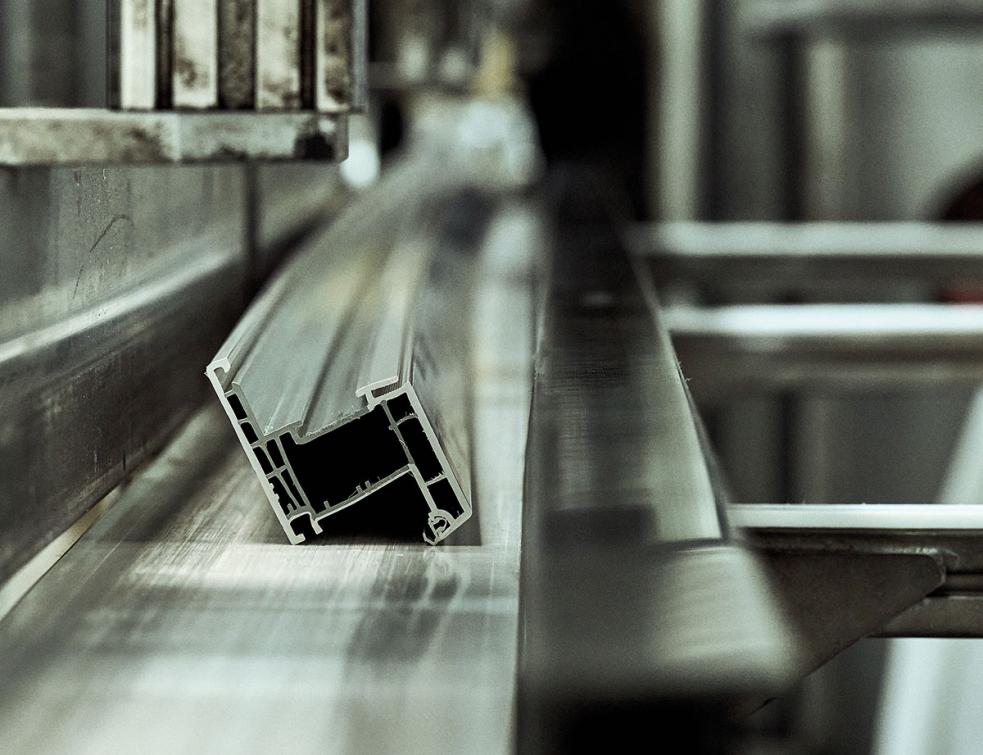
Le processus d’extrusion dans la menuiserie fait face à plusieurs nouveaux défis pour répondre aux attentes du marché : de l’impact environnemental à l’optimisation énergétique...
... en passant par une tendance lourde à la personnalisation de la demande qui requiert beaucoup de flexibilité.
Édouard Guinotte, président du Groupe ASG dévoile une piste pour faire face aux nouveaux défis du secteur : « Les fondamentaux de l’extrusion n’ont pas vraiment évolué et agissons à ce titre sur l’aval et l’amont. Nous sommes ainsi en phase de construction d’une fonderie aluminium (Aluminium Fonderie France) afin de pouvoir mieux maîtriser notre amont et mettre à disposition de nos clients une chaîne de recyclage en boucle fermée, y compris en ce qui concerne la fin de vie. Nous avons atteint, grâce à ces billettes et profils en aluminium, une empreinte carbone divisée par trois ». D’une manière générale, les enjeux majeurs se situent autour de la réindustrialisation et du maintien des compétences. Sur l’extrusion à proprement dite, pas de révolution, mais la maîtrise de l’énergie est devenue cruciale avec des process grands consommateurs d’énergie dans un contexte inquiétant des prix, ajoute Edouard Guinotte : « Nous ne savons pas encore par quoi va être remplacé le contrat ARENH qui prend fin en 2025, de même pour le gaz nous n’en savons pas beaucoup plus. Nous avons besoin de stabilité sur les coûts de l’énergie pour avoir de la visibilité ».
© Profils Systèmes - Avec l’installation d’une seconde presse d’extrusion (ci-dessus) dernière génération d’une puissance de 2 500 tonnes et de 2 200 tonnes pour la première (ci-dessous), le gammiste aluminium montpelliérain Profils Systèmes s'est doté de capacités de production de 2 x 12 000 tonnes/an
Des interrogations qui poussent les industriels vers des process plus économes. Aymeric Reinert, directeur général de Profils Systèmes y voit une évolution majeure : « Le process n’a pas changé dans l’extrusion, par contre les équipements évoluent sans cesse pour diminuer l’empreinte carbone. Nous avons investi dans des fours plus performants et essayons régulièrement de recourir au retrofit ». Une diminution de l’empreinte carbone notamment encouragée dans le monde de l’aluminium par la mise en place du Label Alu+C- du SNFA.
© Deceuninck - Pionnier écoresponsable, Deceuninck annonce recycler 45 000 tonnes de matière par an sur son site dédié à Dixmude en Belgique, et revendique en moyenne 48 % de produits recyclés
La démarche concerne tout le monde, confirme Mickael Areias, directeur industriel chez Deceuninck France : « La RSE est au cœur de la stratégie d’entreprise. À long terme (5-6 ans), nous aurons investi près de 15 M€ sur notre site de Roye (80) pour installer des extrudeuses moins énergivores grâce à des résistances de nouvelle génération et côté infrastructures, avec l’installation de panneaux solaires… ». Une consommation d’énergie qui, pour Jean-François Dreidemy, directeur industriel et directeur général de profine France, est depuis plusieurs années, bien maîtrisée : « Nous sommes classés comme une industrie consommatrice d’énergie, mais avons pris les choses en main. Par exemple, la table de calibrage très énergivore optimise sa régulation par la mise en place de nouvelles pompes démarrant uniquement en fonction des besoins, nous permettant d’économiser 90 % d’énergie ! ».
Sepalumic renforce son industrialisation
© Sepalumic
À Genlis (21), Sepalumic a investi 30 M€ dans l’extension de son usine alimentée en grande partie par une ferme solaire d’une puissance d’1 Mwc, pour y intégrer une nouvelle ligne d’extrusion. Olivier Cros, directeur général de Sepalumic, le rappelle : « Chez Sepalumic, nous souhaitons avant tout dire non au standard et oui au savoir-faire avec des outils de pointe ». Soutenu par le Groupe Valfidus, l’industriel qui intègre la triple compétence – conception-production-distribution – a récemment installé une nouvelle presse hybride de dernière génération qui va consommer moins de 30 % d’énergie par rapport aux presses précédentes. Et anticipe une seconde ligne d’extrusion. Depuis son siège à Mouans Sartoux (06) et son centre R&D, Sepalumic poursuit son travail d’évolution de ses outils et d’autres matériaux.
La coextrusion se généralise
Si le contrôle de la consommation énergétique participe à la baisse de l’empreinte carbone, d’autres pistes sont explorées par les industriels. À commencer par le développement de lignes de coextrusion afin de permettre d’intégrer dans les profils de la matière recyclée. Mickael Areias se félicite de ce virage : « Nous développons énormément les lignes de coextrusion. Ainsi à la fin de l’année, cinq lignes de coextrusion vont nous permettront de travailler sur notre nouvelle gamme de profilés Elegant ThermoFibra Infinity et Elegant Infinity, qui intègre de la fibre de verre continue dans le profilé lui-même, garantissant le meilleur rapport robustesse, performance et écologie ». Deceuninck annonce recycler 45 000 tonnes de matière par an sur son site dédié à Dixmude en Belgique. « Nous revendiquons en moyenne 48 % de produits recyclés grâce à une boucle fermée que nous maîtrisons avec l’utilisation d’un maximum de matière recyclée dans le cœur de nos produits, tout en conservant les mêmes performances », ajoute Mickael Areias. Une volonté d’accélérer sur l’intégration de matière recyclée qui fait de la coextrusion un passage obligé.
© Deceuninck - À long terme (5-6 ans), Deceuninck aura investi près de 15 M€ sur son site de Roye (80) pour installer des extrudeuses moins énergivores grâce à des résistances de nouvelle génération. Deceuninck, qui totalisera cinq lignes de coextrusion, mise sur sa nouvelle gamme Elegant ThermoFibra Infinity
Jean-François Dreidemy confie pour sa part : « profine est sur un grand projet d’entreprise pour accélérer l’intégration de matière recyclée. Nous investissons 10 M€ pour que 50 % de notre parc de machines se retrouve en coextrusion d’ici l’été 2025 ». La difficulté pour réaliser cette coextrusion étant de trouver la matière recyclée, d’où l’importance de faire revenir les produits en fin de vie dans la filière menuiserie pour recyclage. « Le vrai frein, c’est la disponibilité de la matière recyclée », confirme Jean-François Dreidemy. « La matière recyclée doit être de qualité car nous ne pouvons pas introduire tout type de PVC. Un des challenges pour les prochaines années est vraiment de mieux travailler sur la fin de vie en massifiant notamment les points de collecte. Nous sommes chez profine en mesure de récupérer les anciennes menuiseries ». Pas question pour autant de passer à des produits uniquement à base de recyclé, tempère Aymeric Reinert : « Il faut disposer d’une offre diversifiée en proposant les deux types de produits, de la première fusion et du recyclé fin de vie par exemple », relève le dirigeant de Profils Systèmes.
© Profils Systèmes - Avec la diversité d’une gamme référente sur son marché et plus de 5 000 filières, chacune nécessitant l’expérience d’au moins 10 ans d’un régleur de filière où seule la transmission tient lieu de formation, les compétences de haut niveau nécessite un tuteur émérite interne, comme ci-dessus chez Profils Systèmes
Mieux maîtriser le recyclage
© Olivier Toussaint - Rehau conserve le secret de sa recette de PVC recyclé
Avec des interrogations qui demeurent, souligne Emmanuel Mayer, directeur de l’usine de Morhange (57) chez Rehau Window Solutions France : « Tout l’enjeu est de savoir si nous pouvons recycler l’ensemble des déchets de production, qu’il s’agisse d’un déchet de démarrage de production ou qu’il soit issu du démontage d’anciennes menuiseries. Chez Rehau, nous fonctionnons en boucle fermée, donc nous récupérons chez nos clients, sous forme de granulés, l’immense majorité de leurs chutes de production et des produits en fin de vie ». Avec des nouveaux défis dans la gestion des produits en fin de vie sachant qu’ils peuvent contenir de la stérate de plomb, ce qui demande une réflexion plus approfondie pour leur réutilisation. Une pratique encadrée par la législation européenne. Chez Rehau, une des dernières évolutions est de proposer une extrusion blanc cœur blanc contrairement aux habitudes qui sont plutôt avec un cœur gris. Les technologies évoluent dans la coextrusion, observe Emmanuel Mayer : « Il y a dix ans, la coextrusion s’effectuait grâce à une technologie de mélange. Aujourd’hui, nous sommes sur une technologie en couche épaisse, ce qui permet d’obtenir l’intérieur en blanc ou gris et l’extérieur en blanc ou teinté. Cela nous permet surtout de porter le taux de recyclé dans nos produits à 74 % minimum. En revanche, c’est une véritable orfèvrerie d’un point de vue technique ». Des procédés de coloration en ligne ont également été développés pour teinter des recyclés blancs en plusieurs couleurs et accueillir au final un profilé très ressemblant à un profilé monobloc.
Un enjeu sur le recyclage qui existe aussi dans l’aluminium, confirme Jérôme Semay, directeur général d’Installux et du pôle Industrie du Groupe : « Il y a depuis longtemps une attente forte autour du bas carbone, mais la prise en compte de l’aluminium recyclé est devenu aujourd’hui un impératif ». La difficulté réside dans le fait que les aluminiums recyclés peuvent présenter des caractéristiques différentes. Il est donc essentiel de distinguer les aluminiums "propres" issus de process, sans laquage, ni pollution, aux propriétés proches de l'aluminium primaire, des aluminiums en fin de vie qui ont déjà été utilisés. Autant d’interrogations autour des matières recyclées qui ont pour objectif de garantir des produits de qualité en accord avec les attentes des clients. Laissant de belles opportunités de progression dans les années à venir grâce à au développement de l’industrie 4.0 qui a pour grand avantage de sécuriser le process.
Rehau version 4.0
© Rehau
Profiter de la technologie pour mieux produire, c’est le pari dans lequel s’est lancé Rehau à l’image des investissements effectués sur le site de Morhange. Emmanuel Mayer détaille : « Sur l’usine de Morhange, nous avons trois grands sujets actuellement. Premièrement, la smartification des process de pesées de nos préparations. Des modules dotés d’algorithmes interprètent les pesées pour garantir la conformité du produit ». Une façon de détenir la meilleure "recette" de façon automatique. Deuxième sujet, l’équipement d’une ligne de pilotage autonome réalisé en 2024, qui dès cette année, va nécessiter l’assistance d’un seul opérateur. « L’algorithme est lancé et l’IA va indiquer à quel moment passer aux différentes étapes », précise Emmanuel Mayer, abordant le troisième sujet d’actualité : la surveillance, avec des caméras et des moyens de contrôle signalant toute dérive permettant d’agir pour ajuster. « C’est un système de flow control, lequel, couplé à l’algorithme, va pouvoir surveiller la sortie de filière, l’état de surface et la sortie de ligne ».
Sécuriser le process
Jean-François Dreidemy croit aux vertus de cette nouvelle industrie : « L’évolution de nos métiers s’oriente clairement vers l’industrie 4.0. Nous utilisons des machines de plus en plus intelligentes avec des contrôles numériques grâce à une multitude de capteurs nous informant en temps réel ». Ce qui représente une réelle valeur ajoutée et l’assurance de produits de qualité.
© profine - profine investit 10 M€ pour atteindre un parc machines à 50 % équipé de coextrudeuses d’ici l’été 2025
Des axes de travail qui se généralisent, confirme Jérôme Semay : « Notre axe de travail porte sur la productivité et l’amélioration continue. L’évolution des process consiste à rechercher de la productivité 4.0 avec un interfaçage de nos lignes d’extrusion et de nos ERP. L’enjeu se trouve dans l’intégration de l’intelligence partout où nous pourrons le faire ». Avec comme fil conducteur, la recherche d’une augmentation de la productivité et surtout, une sécurisation du process. C’est le sens de l’histoire, fait remarquer Jean-François Dreidemy chez profine : « Grâce à l’IA, le process devient plus constant qu’auparavant, avec des plages de fonctionnement réduites ; mais n’oublions pas que le process d’extrusion reste encore dépendant des hommes ».
Les opérateurs se doivent donc d’être formés ces dernières années ; avec un virage majeur et l’évolution du métier due à la généralisation des outils numériques et digitaux, et l’arrivée de l’Intelligence Artificielle, détenant de nouvelles armes de séduction pour attirer les jeunes recrues dans des métiers en souffrance de candidats.
Geplast optimise ses process de coextrusion
© Geplast
Pionnier et chercheur de matériaux écoresponsables, avec ses 30 lignes d’extrusion, Geplast consacre 40 % de sa production en matière recyclée, soit 2394 tonnes à l’année. Le fabricant s'engage activement à renforcer son modèle durable en investissant dans de nouvelles technologies et en optimisant ses processus de production.
« Grâce au procédé de coextrusion, Geplast propose ainsi des produits en bicouche où la face cachée est constituée de 80 % de matière recyclée, ce qui réduit l'usage de matériaux vierges. La peau externe est composée de matière vierge, garantissant les caractéristiques techniques », informe la porte-parole de l’industriel, qui poursuit : « Nous visons une augmentation significative du taux de matières recyclées avec l’objectif ambitieux d’atteindre 50 % d’ici 2028, contre 40 % actuellement, soit plus de 2431 tonnes de matières recyclées par an ».
Sur son site à Sévremoine en périphérie de Cholet (49), Geplast prévoit d’investir dans de nouvelles machines dédiées à la coextrusion, et de nouveaux outillages à hauteur d’une enveloppe budgétaire d’1 M€. Par ailleurs, des mesures ont été prises pour améliorer l’efficacité énergétique des machines, avec notamment un système de refroidissement d’eau permettant de réduire plus efficacement la consommation d'énergie, de même que le système de production du vide d'air optimisé sur les lignes d'extrusion.
— Franck Guidicelli
Photo ouverture © Rehau - Chez Rehau Window Solutions France, concepteur extrudeur de profilés recyclés NF largement reconnu, une de ses dernières évolutions porte sur une extrusion blanc cœur blanc, contrairement au cœur gris habituel