Décarbonation : les industriels à la recherche de la solution idéale
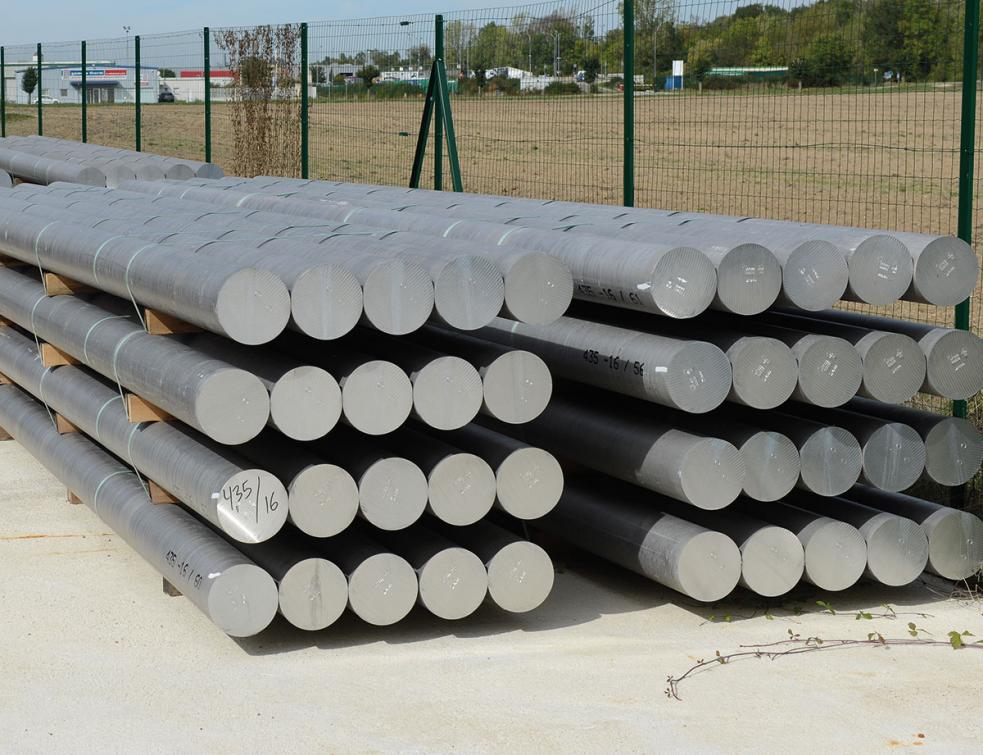
Aiguillonnés par les nouvelles règles européennes en matière de décarbonation, les industriels du verre et de la menuiserie conçoivent de nouveaux matériaux, ...
Publi-Information
... améliorent leur outil de production et la distribution de leurs produits. Radioscopie.
© Profils Systèmes - D.R. - Pour soutenir le volet économique de sa politique RSE, Profils Systèmes a investi 25 M€ au cours des 4 dernières années, notamment dans une deuxième presse d’extrusion en janvier 2024. Cela a permis la création de 40 emplois directs. En 2025, Profils Systèmes projette d’installer un compacteur pour les emballages cartons qui va permettre une réduction drastique des transports avec une relève des déchets une fois par mois au lieu d’une relève quotidienne
Pour décarboner, les gammistes s’organisent. Profils Systèmes a recruté un chargé d’Environnement. Et, depuis 2018, la société montpelliéraine satisfait à la démarche Alu+C- pour ses menuiseries aluminium. Forte également des certifications Qualité ISO 9001, Sécurité ISO 45001 et Environnement ISO 14001 en 2021. Et dernièrement Cradle to Cradle® - C2C - Bronze, pour ses gammes de profilés fenêtres et coulissants Cuzco® et murs-rideaux Tanagra®.
« Nous avons également lancé une démarche volontaire avec le French Business Climate Pledge : il s’agit de tenir des engagements pour réduire notre empreinte carbone. Nos démarches sont synthétisées sur un document que nous remettons à nos clients », souligne Aymeric Reinert, directeur général de Profils Systèmes.
© Sepalumic - D.R. - L’usine d’extrusion de Sepalumic à Genlis (21) bénéficie d’équipements de dernière génération. Le choix d’investir en faveur d’une presse hybride a permis de réduire à hauteur de 30 % la consommation en énergie en comparaison d’une presse traditionnelle
Pour sa part, Sepalumic a initié une démarche de décarbonation touchant chacun de ses trois métiers : la conception, la production et la distribution de ses systèmes de menuiserie aluminium. Ainsi, le bureau d’études et le service achats collaborent avec les fournisseurs. « Nous les invitons à nous fournir des rupteurs de pont thermique en polyamide recyclé aussi performants que les précédents », indique Quentin Rodde, directeur marketing communication et stratégie Fabricants de Sepalumic. Mais la résistance à l’effort du nouveau matériau doit être certifiée par le CSTB, ce qui demande du temps.
Intercalaires warm edge : nés pour économiser l’énergie
Ayant développé leurs propres solutions d’intercalaires warm edge pour les vitrages isolants dès leur création, Edgetech (filiale de Quanex Building Products Corporation) et Technoform Glass Insulation possèdent toutes les deux un ADN naturellement tourné vers les économies d’énergie et le développement durable. Depuis 1989, les intercalaires Super Spacer® d’Edgetech améliorent l’efficacité énergétique des systèmes de vitrage isolant dans le monde entier.
Technoform Glass Insulation innove aussi pour décarboner : « Dès 2019, lorsque les normes française et européenne pour mesurer l’impact carbone d’un produit ont enfin été harmonisées, nous étions les premiers à publier les analyses de cycle de vie (ACV) de notre espaceur warm edge sur la base INIES », relève Thibaud Durousset, directeur commercial et développement France de Technoform Glass Insulation. En sortant sa solution warm edge à base de polypropylène biosourcé dès 2019, Technoform a suscité beaucoup d’intérêt, mais n’a jamais rencontré de demande concrète. Néanmoins, le groupe a poursuivi sa politique de décarbonation : il s’apprête à publier de nouvelles ACV, remises à jour cet été, sur la base INIES. Elles seront accessibles à tous d’ici à fin 2024.
« Entre temps, nos concurrents ont sorti leurs valeurs et en les comparant aux nôtres, nous constatons que nous sommes toujours les plus vertueux du marché en warm edge, de 32 % par rapport à un concurrent qui a publié sur la base INIES. Et même 75 % de mieux sur l’empreinte carbone sur l’ensemble des étapes de production comparativement à un espaceur aluminium. Cet écart provient des matières premières utilisées, du design du produit et du process de production », assure Thibaud Durousset.
De grands bonds en avant ont été réalisés ces 40 dernières années pour améliorer l’efficacité énergétique des fenêtres. Mais, aujourd’hui, chaque amélioration minime sur le warm edge coûte de plus en plus cher aux différents acteurs du marché dont les produits présentent des performances très proches.
« Nous avons atteint une limite sur le warm edge qui correspond bien aux besoins sous nos climats. Conséquence : nous ne sommes plus dans la course à la performance thermique des produits. Les fabricants de fenêtres s’intéressent davantage à la solution warm edge la plus productive et fiable sur le long terme et qui leur offre la plus faible empreinte carbone tout en étant maîtrisée en coût pour faire baisser leurs prix dans le cadre d’une production de masse », analyse Thibaud Durousset.
De son côté, Edgetech prépare plusieurs nouveautés… « Nous allons élaborer des produits qui limiteront l’empreinte carbone, à la fois sur ce que l’on fait, sur ce que l’on fabrique et sur ce que l’on vend. L’élaboration, le transport et le packaging de notre Super Spacer® peuvent encore progresser. Des réflexions importantes sont en cours », dévoile Fabrice Keller, Edgetech Area manager France et Balkans.
© Technoform Glass Insulation - D.R. - Dernier né de Technoform, le SP 31 devrait être commercialisé en France à la fin de l’année 2024. Ce nouvel intercalaire warm edge est compatible avec les machines déjà utilisées par les autres générations d’espaceurs Technoform. Il n’y a pas d’investissements machines à prévoir pour les industriels
© Technoform Glass Insulation - D.R. - « Pliable à froid, le SP 24 offre la meilleure valeur thermique du marché dans sa catégorie tout en offrant une productivité optimale », selon Thibaud Durousset, directeur commercial et développement France de Technoform
Technoform Glass Insulation travaille actuellement à une nouvelle solution optimisée, nommée SP31. Présentée à Batimat, elle devrait recevoir son Document technique d’application (DTA) du CSTB pour la fin de l’année 2024. « Mais nos solutions SP14 – leader du marché – et SP18 offrent des performances assez proches et sont déjà disponibles », rappelle Thibaud Durousset.
Lors de glasstec, Edgetech a surtout mis en avant la durabilité et la flexibilité de ses produits Super Spacer® et T-SpacerTM SG®. Ce dernier est un intercalaire warm edge sans métal, à base de silicone en mousse structurelle avec un dessiccant intégré. Il offre une faible conductivité thermique, affichant 0,19 W/m².K.
« Sa flexibilité permet aux grands vitrages, doubles et triples, qui équipent les façades d’absorber une partie des contraintes de l’effet de pompage engendrées par le vent et la pression atmosphérique. Conséquence : le vitrage dure plus longtemps. Il pourrait n’être remplacé que deux fois plutôt que trois au cours de la vie d’un bâtiment, ce qui amène à utiliser moins de matière première », se félicite Fabrice Keller.
Fineo : la révolution du vitrage sous vide est en marche
Et si, à terme, on ne changeait plus du tout les vitrages des bâtiments? C’est la piste proposée par Fineo, un vitrage sous vide élaboré par AGC Glass grâce à une technologie imaginée par Panasonic pour fabriquer… des écrans plasma pour les téléviseurs.
© AGC Fineo Glass - D.R. - « Nous produisons annuellement 75 000 m² de double vitrage Fineo Glass sous vide. D’ici à la fin 2025-2026, nous ambitionnons de doubler ce volume de production pour passer à 150 000 m² », révèle Xavier Flasse, directeur des ventes de Fineo France
« Actuellement, Fineo est le seul vitrage sous vide disponible sur le marché français qui bénéficie d’un Avis Technique. Avec une épaisseur de seulement 8 mm, il permet de recourir à des châssis très fins et d’alléger les façades tout en offrant des performances équivalentes, voire meilleures, à celles des triples vitrages. Nous sommes aujourd’hui à 0,7 W/m².K et nous voulons nous approcher de 0,44 W/m².K. Fineo diminue par deux le volume de matière nécessaire à la fabrication du châssis et donc le coût environnemental de ces applications. Dépourvu de butyle et des éléments organiques que l’on trouve dans les double ou triple vitrages, Fineo pourrait passer 60 ans dans un bâtiment sans voir ses performances – thermique ou phonique – altérées. Les tests de durabilité réalisés le démontrent. En fin de vie, ce vitrage sera recyclable à 100 % et renaîtra donc à l’infini », indique Xavier Flasse, directeur des Ventes de Fineo France.
Particulièrement adaptée aux bâtiments anciens classés, la solution Fineo est employée dans 80 % des cas dans le cadre d’une rénovation ou d’une restauration. Et il n’est pas non plus nécessaire de systématiquement changer la menuiserie d’origine : « Nous conservons l’ancien châssis, qui doit être en bon état et nous remplaçons simplement le verre d’antan par notre vitrage sous vide, sans toucher à la structure et sans entreprendre de rénovation lourde », précise Xavier Flasse.
© AGC Fineo Glass - D.R. - À Bruxelles (Belgique), l’immeuble de bureaux neufs Belliard est situé dans le très fréquenté quartier européeen. Grâce au vitrage sous vide Fineo Hybrid, il a été possible d’atteindre une atténuation acoustique très élevée dans une épaisseur limitée, permettant d’augmenter l’espace à l’intérieur du bâtiment
Pour l’heure, deux éléments ralentissent encore la diffusion de Fineo. D’abord son prix, ensuite, son mode de production. Alors qu’une ligne classique élabore un double vitrage en 40 à 60 min., Fineo nécessite 20 h de travail en salle blanche afin d’éviter les poussières, sa fabrication se déroulant à l’échelle du micron, soit le millième de millimètre. Mais tout cela pourrait bientôt s’améliorer…
© AGC Fineo Glass - D.R. - Les vitrages simples de cette magnifique villa située à Bruxelles ont été remplacés par Fineo, ce qui a permis de garder les cadres existants. Les fenêtres de style ancien ont été conservées pendant les travaux de rénovation, laissant à la maison son caractère d’antan
« Nous produisons annuellement 75 000 m² de double vitrage sous vide. D’ici à la fin 2025-2026, nous ambitionnons de doubler ce volume pour passer à 150 000 m². Et à l’horizon 2027-2028, notre objectif est d’atteindre 250 000 m². Nous travaillons déjà 7 jours/7 et 24 h/24. Nous cherchons à la fois à réduire de 25 % la durée de notre processus de production et à augmenter nos volumes en décuplant les lignes de fabrication pour pouvoir être encore plus efficace », annonce Xavier Flasse. Le prix du mètre carré de Fineo pourrait donc baisser grâce à cette meilleure productivité.
AGC a décidé d’accélérer la diffusion de Fineo dans l’Hexagone : « Le marché français est le plus prometteur en termes de volume. En 2023, nous y avons commercialisé 500 m² de vitrages Fineo contre 9 000 m² cette année. Et l’année prochaine, nous espérons atteindre les 20 000 m². D’ici à deux ans, nous estimons que la France deviendra le plus gros marché du vitrage sous vide en Europe en raison de son patrimoine et aussi du fait que les architectes des Bâtiments de France ont une importance clé dans la rénovation », anticipe Xavier Flasse. Très récemment, un partenariat de distribution exclusif a été signé entre AGC et le Groupe Devglass pour la commercialisation du vitrage sous vide Fineo pour la France (NDLR cf. p.18-19 dans ce même numéro).
Les sites industriels limitent leur empreinte carbone
Producteur de verre float, Guardian appartient depuis 2017 au groupe américain Koch. Cinq priorités régissent actuellement son rapport à l’environnement : l’innovation, l’efficacité énergétique, la qualité de l’air, de l’eau et une gestion responsable des ressources.
« Nous cherchons à améliorer notre performance environnementale sur le long terme. Nos fours qui fonctionnent 24 h/24 demandent beaucoup d’énergie pour parvenir à une température de 1 600° C. Et tous les 16 ou 20 ans, les fours doivent être reconstruits. Nous profitons de ces travaux pour amener de nouvelles technologies plus efficaces en terme d’énergie », informe Jonathan Brunette, Stewardship manager chez Guardian.
© Guardian - D.R. - Mis en service fin 2023, le nouveau four de l’usine Guardian Glass de Bascharage (Luxembourg) a permis de réduire de 25 % la consommation d’énergie. C’est actuellement le four le plus économe en énergie de Guardian Glass. Guardian a lancé Nexa, une catégorie de produits à l’empreinte carbone réduite. Si le verre de base de Guardian affiche 9,64 kg de CO2 eq. par mètre carré, Nexa 9 descend à 8,58 kg de CO2 eq. par mètre carré. Nexa 6 atteint même 6,38 kg de CO2 eq. par mètre carré
Depuis 2017, Guardian qui a reconstruit la plupart de ses fours en Europe – Allemagne, Hongrie, Angleterre, Pologne… – a mis en service au 4e trimestre 2023 le nouveau four de l’usine Guardian Glass de Bascharage, au Luxembourg. Fonctionnant 24/24, le four est doté d’un système de récupération de la chaleur qui permet de préchauffer l’oxygène pur et le gaz naturel, il économise environ 25 % de gaz naturel. « Bascharage produit tant du verre float Guardian ExtraClearTM que du verre float Guardian UltraClearTM à faible teneur en oxyde de fer. Les efforts entrepris depuis 7 ans nous permettent de réduire notre empreinte carbone. D’ailleurs, six déclarations environnementales de produits (EPD) viennent tout juste d’être publiées », informe Jonathan Brunette.
Guardian a lancé Nexa, une gamme de produits à l’empreinte carbone incorporé réduit. Si le verre de basefloat standard de Guardian affiche 9,64 kg de CO2 eq. par m², Nexa 9 descend à 8,58 kg de CO2 eq. par m². Nexa 6 atteint même 6,38 kg de CO2 eq. par m². « Les produits verriers de Guardian sont parmi les plus vertueux sur le marché actuellement en Europe. En utilisant plus de calcin, en recourant à des fours plus efficaces énergétiquement et en optimisant tous nos process, nous obtenons du verre présentant des taux de carbone incorporé moins élevés, ce que confirment les fiches EPD qui viennent d’être publiées, tout en préservant la qualité et les performances de nos produits », affirme Jonathan Brunette. Tout récemment, en Angleterre, une entreprise a décidé d’acheter du verre Nexa pour sa teneur réduite en carbone.
La production industrielle de Sepalumic englobe désormais l’extrusion des profils aluminium, leur laquage et leur sertissage. Mise en service en juin 2024, la centrale solaire de 1 MW qui surmonte l’usine d’extrusion de Sepalumic à Genlis (21) couvre environ 20 % des besoins de ce site industriel.
© Sepalumic - D.R. - « Chez Sepalumic, la part d’achat d’aluminium représente près de 80 % du bilan carbone de l’entreprise », rappelle Quentin Rodde, directeur marketing communication et stratégie Fabricants de Sepalumic
« Plutôt que de continuer à nous approvisionner auprès des extrudeurs, principalement espagnols ou italiens, nous avons décidé d’intégrer l’extrusion des profils aluminium. Elle s’effectuera bientôt en 3 x 8 sur notre site de Genlis qui a obtenu la Certification Alu+C- en janvier 2024. Genlis nous permet de mieux maîtriser nos chaînes d’approvisionnement tout en bénéficiant d’une meilleure flexibilité de conception. Nous obtenons aussi plus de réactivité et nous grandissons les compétences de nos équipes en interne », explique Quentin Rodde.
Utiliser des billettes produites par des ressources d’énergies renouvelables telle que l’hydroélectricité a permis à Sepalumic de réduire son empreinte carbone à seulement 4 kg de CO2 par kg d’aluminium produit, soit moins d’un quart de la moyenne mondiale. « Depuis septembre 2023, Genlis produit des billettes 100 % bas carbone et 95 % recyclées, provenant d’aluminium recyclé produit en France. Et nous avons opté pour une presse hybride plutôt que d’investir dans une presse traditionnelle. Nous diminuons ainsi sa consommation en énergie de 30 % », précise Quentin Rodde.
Profils Systèmes n’envisage pas pour le moment de créer sa propre fonderie de billettes d’aluminium. « Nous n’avons pas de fonderie dans le groupe. Nous achetons donc nos billettes auprès de fondeurs du Nord de l’Europe ou de France, dans une moindre mesure car il y en a peu. Nous sommes audités sur la partie environnementale, la partie extrusion sur le choix des billettes et sur les process d’extrusion avec des empreintes carbone maximum qui sont à respecter et qui s’améliorent au fur et à mesure des années », détaille Aymeric Reinert.
© Edgetech - D.R. - Le T-SpacerTM SG® d’Edgetech est un intercalaire warm edge sans métal, à base de silicone en mousse structurelle avec un dessiccant intégré. Il offre une faible conductivité thermique, affichant 0,19 W/m2.K
Pour sa part, Edgetech réfléchit actuellement à l’amélioration de ses outils de production, notamment ceux de son usine de Heinsberg (Allemagne). Inaugurée le 19 mai 2011, elle est la plus en pointe aujourd’hui sur le sujet. « Nous faisons participer des acteurs locaux – plutôt que d’autres situés à l’autre bout de la Terre – pour construire les outils de production que nous utiliserons demain », témoigne Fabrice Keller. Edgetech cherche à limiter les apports en gaz nécessaires à la production d’énergie. Elle achète aussi de l’électricité verte.
Insio®, le nouveau vitrage sous vide Saint-Gobain Glass ouvre une nouvelle ère
© VMA/A.B.
Dévoilé sur le stand de Saint-Gobain à glasstec (du 22 au 25 octobre derniers) à Düsseldorf, le nouveau vitrage sous vide Insio® marque une nouvelle étape dans l’innovation pour une construction toujours plus vertueuse et durable. Commercialisé par le réseau de transformation Glassolutions-Saint-Gobain en milieu d’année 2025 en France, il promet des performances exceptionnelles en matière d’isolation thermique, inférieures à 0.4 W/(m².K) pour sa version Insio® Hybrid, et s’inscrit dans l’engagement du Groupe Saint-Gobain à atteindre zéro émission nette de carbone d’ici 2050.
« Le nom Insio® représente la quintessence de la technologie isolante en combinant INSulation (Isolation) - Innovation (Innovation) et Optimization (Optimisation). Associé à Eclaz® Zen, le vitrage Insio® permettra notamment aux utilisateurs de bénéficier d’une réduction de l’empreinte carbone avec la possibilité de l’associer avec le verre bas carbone Oraé® », informe le porte-parole de la marque.
— A.B.
Limiter l’empreinte carbone de la distribution
Le groupe Technoform aimerait utiliser le train plutôt que le camion pour transporter ses produits d’Ouest en Est. Mais les solutions de fret ne le proposent pas.
Chez Sepalumic, l’usine de Genlis approvisionne les dépôts régionaux du matériel dont ses clients ont besoin un peu partout en France. « En modifiant les tournées de livraison en lien avec nos clients, le nombre de kilomètres parcourus a baissé de 18 % par rapport à l’exercice 2023 », spécifie Quentin Rodde.
Pour sa part, Profils Systèmes maximise le ferroutage : un partenaire de l’entreprise y recourt pour transporter les produits entre le site industriel et le terminal ferroviaire, puis chez les clients. Il s’est équipé pour cela de tracteurs routiers mus au GNV. Avec de tels atouts, la décarbonation est en bonne voie.
Photo ouverture © Sepalumic - D.R. - En faisant le choix de billettes produites par des ressources d’énergies renouvelables telle que l’hydroélectricité, Sepalumic a réduit l’empreinte carbone à 4 kg pour 1 kg d’aluminium produit
L'auteur de cet article
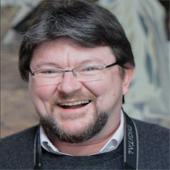