Les défis de l’écoconception
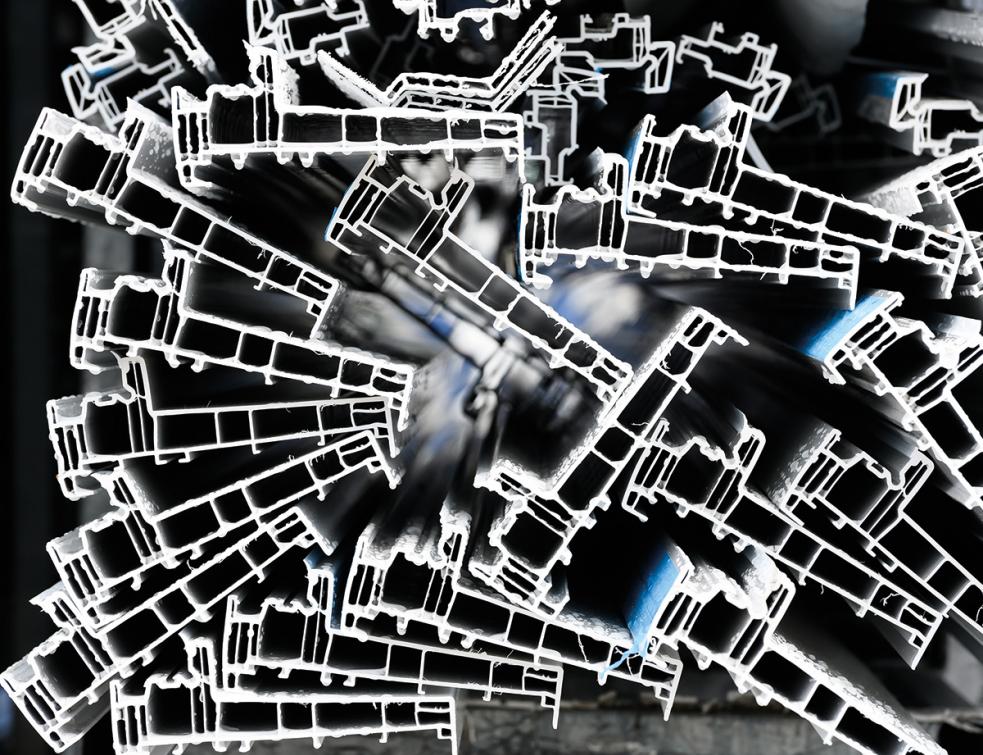
La boucle fermée qui apparaît aujourd’hui comme le graal à atteindre pour tout industriel qui se respecte et respecte son environnement n’est pas si simple à mettre en place.
Au-delà de la collecte de la matière et du déploiement de nouveaux outils industriels, il faut convaincre les acteurs de terrain.
© Hydro Building Systems France - billettes HydroCircal75R
« Impossible de scinder les questions liées aux approvisionnements, à la gestion des déchets, au transport et à la logistique, car seule une approche globale peut porter ses fruits et il s’agit d’abord d’un état d’esprit », déclare d’emblée Christophe Lotz, directeur RSE du Groupe Liébot. « Même en tant que leader de la menuiserie, avec nos 7 sites de production, nous ne pouvons pas œuvrer seuls, nous devons convaincre nos clients et fournisseurs ». Première étape, la décarbonation. « Faut-il agir en priorité sur nos sites industriels ? La réponse est non, car 80 % de notre impact carbone provient de la matière première », constate-t-il. C’est pourquoi le Groupe Liébot, en partenariat avec le Groupe Corre, ouvrira la fonderie Coralium au mois de janvier 2025, avec pour mission de booster son plan de décarbonation. L’usine, construite à Sainte-Hermine (Vendée), permettra de trier les déchets sur site et de produire de l’aluminium bas carbone. « C’est l’avenir, notre objectif est d’en produire 40 000 tonnes par an », précise Christophe Lotz. Le Groupe mène le combat sur plusieurs fronts : embarquer ses salariés via la fresque du climat, motiver ses clients à récupérer les menuiseries lors des travaux de rénovation, ne serait-ce que pour collecter le verre, améliorer la sobriété de ses sites de production, y compris au niveau des emballages …
Stratégie de recyclage
C’est également une approche globale que Schüco a présenté l’année dernière : Schüco Carbon Control. « Une boîte à outils pour concevoir, construire, exploiter et recycler le bâtiment bas carbone », résume Alexandre Krupka, directeur prescription de Schüco. À date, en moyenne assure-t-il, « les gammes Schüco intègrent de 50 à 60 % d’aluminium recyclé ». Un pourcentage qui doit augmenter. « Nous mettons en place une stratégie de recyclage pour aider nos partenaires qui nous confient n’avoir ni le temps, ni les ressources pour déposer les menuiseries en fin de vie chez un recycleur. Nous avons investi dans des chevalets, noués des accords avec les démanteleurs et avec une fonderie, afin de collecter la matière. Un premier test est en cours dans le nord-est de la France », explique Stéphane Billaud, animateur du réseau Partenaires référence Schüco France. Et d’ajouter : « Nous souhaitons accompagner nos partenaires à entrer dans une démarche de décarbonation de leur propre activité, à recycler les menuiseries en utilisant notre label Schüco Carbon Control Partenaires engagés, et in fine à promouvoir nos produits à forte performance ».
L’aluminium serait recyclable à l’infini. « Le défi qui se pose à nous est d’optimiser les process en boucle fermée, nous sommes membres du SNFA et encourageons nos clients à utiliser Valobat, car c’est un moyen de mieux flécher les démanteleurs », rappelle Aymeric Reinert, directeur général de Profils Systèmes. « Les progrès réalisés dans la collecte, le tri et la traçabilité des déchets d'aluminium post-consommation, ainsi que le processus d'extrusion permettent à Technal de fabriquer ses produits en Hydro CIRCAL® 75R et donc de réduire son empreinte carbone qui est de 1,9 kg de CO2e/kg d'aluminium, contre 2,2 auparavant », se félicite de son côté Pascal Violleau, responsable prescription de Technal.
© SNEP - Recyclage des matières PVC
Dans le secteur du PVC, les grands industriels pratiquent déjà le recyclage de leurs chutes de production. « Le secteur du PVC est en ordre de marche pour développer le recyclage, le savoir-faire industriel est au point, le grand défi provient de la gestion de la déconstruction sur le marché du diffus, c’est toute la problématique de la REP », note Sylvain Gaudard, responsable communication du SNEP.
profine s’organise depuis plusieurs années et travaille avec 14 partenaires. L’objectif étant de parvenir à harmoniser les process : « Les fenêtres PVC collectées sont prébroyées aux quatre coins de l’Europe, les déchets étant orientés vers des centres capables de trier le métal, la couleur… avant d’être acheminés vers le centre de recyclage du Groupe à Pirmasens », détaille Claude Lickel, directeur commercial et marketing de profine. Car pour lui, « un autre gros défi du recyclage vient du transport et de la logistique ». Le nouvel outil, basé à Pirmasens en Allemagne, a ouvert ses portes au mois de janvier avant d’être inauguré le 1er mars. « profine développe une approche européenne en centralisant ses ressources afin d’optimiser la logistique », argumente-il. Ce centre affiche une capacité de production de 15 000 tonnes par an. Les matériaux PVC issus de menuiseries en fin de vie sont achetés auprès de sociétés externes qui procèdent à un prébroyage et un tri grossier. Ils sont ensuite soumis à un processus de nettoyage et de filtrage en plusieurs étapes, afin d'obtenir des granulés de haute qualité, qui seront réemployés dans les profilés de fenêtres avec de la matière vierge. « Ce PVC recyclé sous forme de granulé assez homogène sert à produire la matière injectée à l’intérieur des produits, alors que la matière vierge blanche est employée à l’extérieur », souligne Claude Lickel. Cette nouvelle installation permettra à l'avenir de recourir de manière plus flexible aux matériaux recyclés et de contrôler plus précisément la qualité des matières premières recyclées. « Aujourd’hui, notre production ingère 13 % de matière recyclée, l’objectif étant d’atteindre les 25 % fin 2025 », avance-t-il.
Roland Besnard, président du Groupe Bouyer Leroux
1. Quelle est votre stratégie en matière environnementale ?
Notre stratégie est écrite depuis une quinzaine d’années, et nous la questionnons régulièrement. Elle consiste à apporter à différents profils de clientèle des solutions écoperformantes permettant de construire et de rénover un habitat sain, économe en énergie. Elle repose sur l’utilisation optimale des ressources (matières premières, énergie, eau). Il s’agit de produire mieux, plutôt que plus.
Depuis trois ans, nous établissons notre Déclaration de Performances Extra-Financière (DPEF) et nous la renforçons en vue de la CSRD (NDLR - Corporate Sustainability Reporting Directive, la directive européenne visant à harmoniser le reporting extra-financier) avec plus d’indicateurs communs à toutes les sociétés, et le renforcement de la frugalité dans son acception la plus large.
Nous menons des projets transverses, par exemple une production d’électricité plus verte à horizon 2030 pour laquelle nous déployons des installations photovoltaïques, ainsi qu’une réduction de nos consommations électriques.
2. Quelle place occupe l’écoconception dans votre Groupe ?
Cette dimension entre dans le pilotage des projets du Groupe, via nos cinq activités, dans les solutions constructives en terre cuite, dans la fermeture de l’habitat, dans nos spécialités bétons, les écosolutions de parquets de Panaget et la valorisation énergétique. Nous avons constitué une équipe, en charge de cette dernière activité, autour du directeur énergie et environnement, certaines compétences du service R&D, un ingénieur thermique. Mon objectif étant de faire de la CSRD un outil de pilotage de l’amélioration continue et de la frugalité.
3. Et concrètement, quelles sont les avancées dans les activités fermeture et menuiserie ?
Nous concevons des solutions bioclimatiques (screen, pergola) et intégrons des matières recyclées (matières plastiques, aluminium). Par exemple, la production de SPPF utilise environ 60 % de matières issues de la filière recyclage. D’ailleurs nous travaillons, pour SPPF et Groupe Maine, en circuit fermé, en broyant la matière issue des déchets de production. Le PVC est en avance.
Les équipes ont été formées à l’écoconception. L’offre évolue, le bloc-baie Chrono One de Soprofen contient une partie de matière regénérée par exemple. SPPF développe actuellement un bloc-baie (Green Bloc) avec une dimension ecofriendly.
Nous avons conçu un appui de fenêtre issu d’un partenariat entre l’activité fermeture et l’activité terre cuite de notre groupe, afin de faciliter la mise en œuvre et d’améliorer la fixation des menuiseries à un point souvent source de déperdition thermique. Cette gamme d’appui de fenêtre allégé Thébault, Lisa, est préfabriquée et offre une qualité de finition lisse.
Disponibilité de la matière & écocircularité
Le fabricant français Isosta de panneaux sandwich, façades et de soubassements de menuiserie, s’est doté de sa propre ligne de démantèlement de panneaux sandwich, Repan. « En 2023, nous avons récupéré 200 tonnes de matière, issue des chutes de production provenant de nos sites et de chez nos clients industriels, un peu moins qu’attendu », consent Christophe Molliex, directeur RSE chez Isosta. Les panneaux en fin de vie ne seraient, pour l’instant, ni identifiés, ni en état d’être recyclés.
© Isosta Repan - Isosta Repan, panneaux collectés en attente de déconstruction
Isosta projette de créer un Repan 2 avec une capacité de production plus élevée. « L’entreprise a acheté une friche industrielle à Sens avec un bâtiment de 5 000 m² lui permettant d’accueillir les installations nécessaires à la séparation des matières et de passer à la vitesse supérieure », commente Christophe Molliex.
Pour tenir leurs objectifs, les industriels doivent dénicher de la matière. « Les chutes de production de nos clients ne représentent qu’environ 1,5 tonnes de matière par an, et la collecte se heurte au cycle de vie de la fenêtre, et au manque de fenêtres PVC à démonter », remarque Claude Lickel. profine mise sur la répartition de l’utilisation de la matière recyclée.
« Au lieu d’insérer de la matière recyclée dans tous les profilés, nous en mettons un maximum (45 %) dans les 17 profilés les plus vendus », glisse Claude Lickel.
Car la pénurie de matière ralentit la production en boucle fermée. Plusieurs questions se posent : la collecte, mais aussi la qualité du matériau. « Nous pouvons recycler la matière issue de la déconstruction des fenêtres à condition de pouvoir justifier de sa traçabilité, la réglementation limite en effet le taux de plomb qu’elle contient, suivant son origine, l’utilisation de la matière se cantonne à certaines productions, mais cette restriction représente aussi une chance car elle limite les importations extra-européennes », estime Sylvain Gaudard.
Maelenn Rougié, chargée de mission environnement à l’UFME, évoque Fervam 2 et réaffirme la volonté de la marque de soutenir la boucle fermée
1. Quel bilan pouvez-vous dresser de l’activité de la marque Fervam ?
La marque Fervam, propriété de l’UFME, centre son activité sur la collecte et le recyclage en boucle fermée de menuiserie, avec deux objectifs principaux : l’utilisation de matières premières recyclées pour diminuer l’impact carbone et faire face à la raréfaction des matières. En 2024, il s’agit de massifier l’activité, de consolider l’existant et de densifier le réseau. Adossée à la Charte UFME, Fervam compte plus de 140 signataires, illustrant l’ensemble des activités des acteurs de la boucle fermée (poseurs, fabricants, démanteleurs, recycleurs …).
La marque favorise la communication et la mise en lumière de l’implication de ses signataires.
En 2023, 8 000 tonnes de menuiseries ont été déposées et mises en recyclage.Nous suivons les progressions des quantités, notamment de calcin (multipliée par 2,77 par rapport à 2021) et de PVC (multipliée par 1,94 par rapport à 2021).
2. Vous annoncez une refonte de la Charte…
Oui, nous prévoyons une deuxième version pour renforcer les engagements et sécuriser la boucle fermée. Nous devons y intégrer des évolutions réglementaires, notamment la REP PMCB et la future REP emballages.
La boucle fermée, que n’exige pas la REP PCMB, nous semble essentielle pour la filière menuiserie. Fervam 2 fournira les outils de communication nécessaire à sa promotion.
3. Comment agir au niveau des emballages ?
Nous travaillons à l’identification des pistes pour rationaliser l’utilisation de certains types d’emballages, réemployer les matériaux pour simplifier le tri, mutualiser les collectes.
Réemploi & coextrusion
Pour Veronica Garcia, circularity manager South Europe - Hydro Building Systems, « notre démarche s’inscrit dans la boucle fermée ; évoquer l’écoconception, c’est penser d’abord à la façon de désassembler le produit pour favoriser un, son réemploi ou deux, son recyclage. Notre Groupe a mis en place un système de traçabilité des produits avec un QR code pour améliorer leur entretien et allonger leur cycle de vie, et donner des consignes pour leur valorisation ». Réemployer des menuiseries en fin de vie peut s’envisager en détournant leur utilisation, suggère-t-elle, mais cela nécessite un démantèlement dans les règles de l’art.
« La coextrusion nécessite de mener une réflexion sur le réemploi du produit en fin de vie dès sa conception, car pour les démonter, il faut éviter de lier les matériaux entre eux et les assembler mécaniquement », martèle Éric Chartier, responsable du bureau d’études et de la R&D chez Geplast. Cet expert milite pour l’adoption de bonnes pratiques, car « il n’est pas toujours pertinent d’utiliser de la matière recyclée, en trop faible quantité, on perd le bénéfice ». En mars 2024, Geplast estime à 37 % la part de matière recyclée dans sa production totale et vise les 50 % d’ici deux ans.
La démarche environnementale réserve parfois des surprises. « Des matériaux comme les mousses XPS – mousse rigide de polystyrène extrudé – peuvent être granulées et réinjectées dans la fabrication, ainsi 5 % des matières que nous utilisons proviennent de Repan, c’est peu, mais nous encourageons notre fournisseur pour augmenter cette part », témoigne Christophe Molleix. « Le bureau d’études d’Isosta planche sur le réemploi de l’isolant, inenvisageable jusqu’à présent… ».
© Rehau - Rau-Infinio, une des innovations de Rehau Window Solutions
« Rehau a beaucoup investi en R&D sur de nouveaux matériaux biosourcés qui répondent aux cahiers des charges des fenêtres par exemple, ce qui implique de prendre en compte la totalité de la chaîne de valeur ; nous produisons et concevons les profilés, mais nous devons également conduire nos clients à mener des réflexions sur ce sujet », avoue Maxime Boileau, directeur marketing-communication-prescription Rehau. « Nous sommes concernés par la taxinomie(1), poursuit-il, qui sert à orienter les productions vers la neutralité et nous devons trouver des solutions viables à moyen et long terme, tout en restant dans des niveaux de prix acceptables pour le marché ». Avec une autre exigence : « Nos clients vont devoir investir dans les quinze prochaines années dans de nouvelles machines pour s’adapter, ils sont à l’écoute, à nous d’anticiper pour les guider ». À l’occasion du Salon Fensterbau Frontale 2024, Rehau Window Solutions a présenté ses dernières innovations, avec par exemple des profilés aux propriétés mécaniques exceptionnelles issus de la nouvelle technologie Rau-Infinio : des fibres de verre continues dans une matrice thermoplastique. « Ce nouveau matériau répond aux enjeux de l’écoconception et ouvre de nouvelles possibilités pour les solutions de fenêtres. Il possède des valeurs pionnières en termes de stabilité, d'isolation, de possibilités d'application, de maniabilité, de design, de sécurité et de durabilité », se réjouit Maxime Boileau.
© Geplast - Fourrures tapées coextrudées pour diminuer l’impact environnemental
Geplast multiplie les initiatives. L’industriel commercialise une gamme de fourrures tapées coextrudées - éléments structurels qui se déclinent de 10 mm en 10 mm – avec joint d’étanchéité intégré – pour couvrir les doublages et supprimer les chutes de délignage. « Nous essayons d’agir sur tous les points : par exemple, nous analysons les charges afin d’utiliser Loryza®, matière à base de cosse de riz dans les produits dédiés à la clôture et nous étudions les opportunités offertes par les roseaux qui doivent être coupés régulièrement pour se régénérer et fournissent donc une matière disponible », indique Éric Chartier.
Coextrusion et nouveaux matériaux représentent de nouvelles pistes d’investigation pour verdir le bâtiment.
FenêtréA et MENREC
« Si l’entreprise ne s’engage pas dans une démarche visant la neutralité carbone, elle disparaîtra demain, car elle ne répondra plus aux attentes de la société », avait déclaré dans nos pages Dominique Lamballe, président de FenêtréA, engagé de longue date en faveur de l’écoresponsabilité et cofondateur de MENREC en 2021 avec Atlantem Industries, associant Riou Glass et la société de transport Bohelay spécialisée dans la logistique du recyclage ; en vue de valoriser les différents matériaux des menuiseries en fin de vie (bois, PVC, aluminium et verre) et leur réemploi pour la fabrication de nouvelles solutions (fenêtres, portes et volets). Et stopper leur enfouissement !
Le président de FenêtréA s’est très tôt positionné face aux changements de paradigmes et notamment les enjeux de la décarbonation, visant la neutralité carbone en 2040 dans une démarche de transition via le "Diag Décarbon’action" proposé par BPI France, en partenariat avec l’Ademe. Sur une superficie aujourd’hui de 50 000 m² où se déploie un fort engagement écologique autant que sociétal, la prochaine usine FenêtréA, la plus automatisée d’Europe dans sa filière et 5e unité de production sur le même site de l’entreprise bretonne, viendra s’intégrer en osmose optimale avec son environnement.
A.B.
(1) La taxinomie (ou taxonomie dans les textes européens) publie une liste d’activités contribuant à atteindre les objectifs de l’UE en matière de neutralité carbone en 2025 et de protection de l’environnement. Cette classification doit guider les investisseurs vers des activités "soutenables".
Focus sur le verre plat
© Saint-Gobain Glass - Réception du calcin
« Pour pouvoir recycler du verre plat en boucle courte dans un four float (produisant du verre plat), il est préférable que les fenêtres soient collectées de manière intègre, puis démantelées, afin de garantir le niveau de qualité élevé exigé pour ce type de four », explique l’éco-organisme Valobat sur son site Internet. « L’activité de Valobat monte en puissance, c’est le seul éco-organisme présent sur l’ensemble de la filière, Valobat compte 4 800 adhérents, nous ouvrons des points de reprise toutes les semaines, et en recensons aujourd’hui 1135 », indique Florence Collot, directrice des relations adhérents de Valobat. « Nous signons des contrats avec des déchèteries professionnelles, privées et publiques, et nous les finançons pour qu’ils acceptent les déchets déposés par les entreprises du bâtiment », ajoute-t-elle. Valobat s’est donné un rôle de catalyseur pour contribuer à l’amélioration du recyclage, soutenir le réemploi et accompagner l’écoconception. « Valobat ne se substitue pas aux industriels, mais apporte ses conseils et soutiens financiers ; nous souhaitons agir à tous les stades, y compris en conception pour faciliter le réemploi des produits, faire connaître les initiatives et encourager les industriels à adopter ces nouvelles pratiques », commente Florence Collot.
Valobat s’adresse aux différentes filières de PMCB recyclables (métaux, plastiques, bois, plâtre, matériaux inertes, laines minérales et menuiseries vitrées). Dans le verre plat notamment, les enjeux de démontabilité des produits sont cruciaux, sachant qu’il faut éliminer les perturbateurs. « Nous développons un outil de recyclabilité qui sera mis à disposition en fin d’année et permettra aux industriels de savoir si leurs produits sont recyclables », annonce Florence Collot. D’autres projets sont en cours, comme l’appel à projet "Solutions innovantes de recyclage & valorisation", consultables sur le site Internet de l’éco-organisme.
AGC Glass Europe
© AGC Glass Europe
Marqué par une demande croissante en verre feuilleté, AGC Glass Europe a inauguré le 26 avril dernier, le lancement d’une nouvelle ligne de fabrication de verre feuilleté dans son usine d’Osterweddingen en Allemagne. Cet investissement de première importance constitue pour AGC un atout solide et durable sur un marché porteur et renforce sa démarche cohérente d’écoresponsabilité, puisque l’usine va entamer la production de verre bas carbone (Low-Carbon Glass) au cours des mois à venir. Cette nouvelle ligne contribuera également à optimiser le transport routier en Europe, réduisant ainsi l’empreinte carbone d’AGC par la suppression de l’émission de 1 100 tonnes de CO2 tous les ans.
Vers la boucle fermée
Fabrice Dhalluin occupe la fonction de directeur de l’économie circulaire chez Saint-Gobain Glass France depuis le 1er juillet 2023. La création de ce poste en dit long sur la volonté de l’entreprise de renforcer son engagement. « Nous avons lancé Saint-Gobain Glass Recycling afin de privilégier le recyclage du vitrage en fin de vie en boucle fermée et d’accompagner nos partenaires », affirme-t-il. « En 2023, les usines de Saint-Gobain ont réceptionné 4 000 tonnes de calcin issus de menuiserie en fin de vie, contre 30 tonnes en 2018, mais avec un potentiel estimé à 200 000 tonnes selon l’Ademe ; les progrès sont réels, mais du chemin reste à faire », constate-t-il. L’objectif des 5 500 tonnes fixé pour 2024 devrait être dépassé. Saint-Gobain Glass Recycling rassemble une cinquantaine de partenaires. « Notre objectif étant de proposer une solution de proximité pour le démantèlement, avec un point d’attention spécifique sur la qualité du calcin, afin de pouvoir l’utiliser dans la production de vitrage », précise Fabrice Dhalluin. « C’est pourquoi nous qualifions les partenaires, et que nous envisageons d’étoffer ce réseau afin de réduire les zones blanches, mais sans urgence car notre mission consiste à former les équipes et à les accompagner dans la compréhension de la réglementation ». Le recyclage en boucle fermée doit permettre de produire un verre plat en maintenant les performances et la qualité esthétique de l’offre. « À l’image du premier verre bas carbone, Orae®, qui conserve les mêmes propriétés que le verre clair Planiclear®, alors qu’il réduit de 30 % les émissions de CO2 et bénéficie d’une fiche FDES », assure encore Fabrice Dhalluin.
AGC Glass recycle le calcin provenant de ses usines et filiales et souhaite augmenter le taux de verre recyclé dans ses produits. « À horizon 2030, l’objectif est d’utiliser la moitié de matière recyclée, alors qu’aujourd’hui, la moyenne européenne s’élève à 30 %, sachant que la majorité provient de chutes de production », déclare Antonella Contino, sustainability manager scope 3 program AGC Glass Europe. Comment y parvenir ? « Nous devons aller chercher les vitrages en fin de vie lors de la déconstruction des bâtiments », répond cette spécialiste. En France, le mouvement semble lancé, mais regrette Antonella Contino : « il ne se passe pas grand-chose dans les autres pays européens ».
Les nouveaux produits d’AGC devront pouvoir être recyclés plus facilement, ce sera le cas de Fineo, le premier et seul vitrage isolant sous-vide.
L’entreprise travaille également avec un réseau de partenaires spécialisés dans le démontage des façades et le démantèlement des vitrages, afin de collecter ceux-ci transformés en calcin de qualité (Recycle Glass), pour le recyclage et la refonte dans ses fours de verre plat.
Côté réemploi, les vitrages démantelés en façade n’affichent pas le niveau de performance requis aujourd’hui. Mais ils pourraient être orientés vers d’autres utilisations. « En Finlande », glisse Antonella Contino, « un projet a donné lieu au réemploi à l’intérieur de châssis démontés en façade ». Mais globalement, admet-elle, « la technicité du produit verrier n’autorise guère son réemploi, seul le recyclage en boucle fermée semble fournir une solution intéressante ».
— Véronique Méot
Photo ouverture © Rehau-Paprec