Atelier : ergonomie et productivité, les deux sont liées !
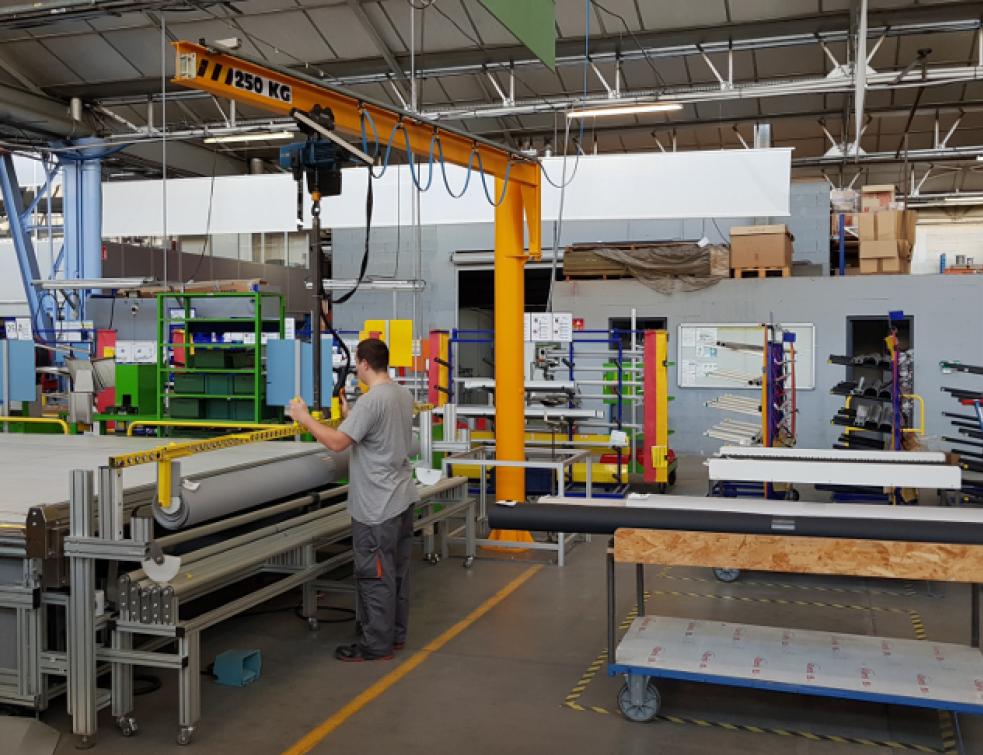
Améliorer les conditions de travail dans les usines est un investissement gagnant-gagnant. car outre la sécurité et la santé des opérateurs.
Car outre la sécurité et la santé des opérateurs, cette stratégie booste les cadences et la qualité, avec en ligne de mire, la satisfaction client. Témoignages.
"Comment une petite entreprise peut-elle aborder le sujet ? "
Le Lean s'est imposé avec l'évolution de notre chiffre d'affaires, mais nous avions besoin d'être accompagné dans cette démarche. Nous avons fait appel à un cabinet spécialisé, Operative. Nous avons ainsi pu identifier les sources de gaspillage et optimiser les flux dans l'atelier, par exemple en matérialisant au sol les emplacements des chariots.
"Quelles sont les difficultés rencontrées ? "
Il faut savoir être pédagogue, expliquer les bénéfices de la démarche, convaincre du bien-fondé de la mise en place de procédures. Nous avons instauré un point quotidien avec les équipes afin de corriger les écueils. L'objectif étant que les postes de travail soient alimentés en permanence, afin d'éviter les ruptures. Nous veillons ainsi à ce que l'opérateur chargé des débits remplisse les différents chariots en matière correspondant à un temps de travail précis. Chacun sait ainsi ce qu'il a à faire et quand. Il s'agit d'adapter les ressources aux besoins, selon le principe du Kanban, la gestion de stock juste à temps.
"Quels sont les résultats ? "
Nous avons gagné en productivité, nos investissements ont été rentabilisés assez rapidement. Le temps de présence des salariés équivaut à plus de 90 % à un nombre d'heures réellement travaillées et donc facturables.